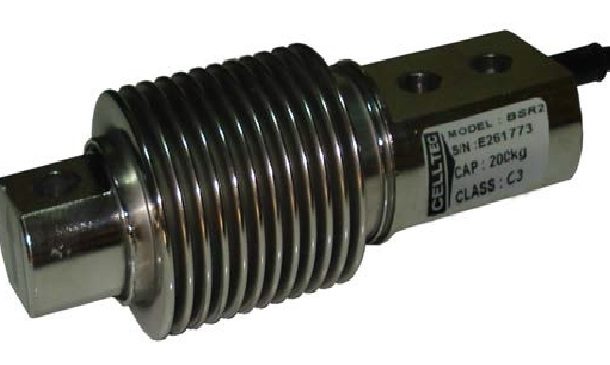
- ۰۲۱-۸۸۰۳۵۹۲۴
- kian.industry.t@gmail.com
- ۰۹۱۲-۱۵۴۹۶۶۸
- خانه
- محصولات
کیسه و پاکت پرکن
تولید دستگاه های پرکن اتوماتیک و نیمه اتوماتیک در کیان صنعت برای سیمان، مواد غذایی، مواد پودری ریز و درشت، مایعات با سیستم های توزین
سیستم های توزین و اختلاط
استفاده از لودسل های با کیفیت در سیستم های توزین و نرم افزار های ویژه کنترل و مانیتورینگ در کنار ماشین آلات اختلاط اتوماتیک
نگهداری مخازن
نگهداری مواد پودری مانند سیمان و مواد پتروشیمی در مخازن و هاپرها استفاده از فشار هوا مانند ایربلستر و شوک بلستر و فیلتر های کیسه ای
- درباره ما
- گالری
- اخبار و مقالات
- تماس
- العربیه
- English
- کوردی
Menu